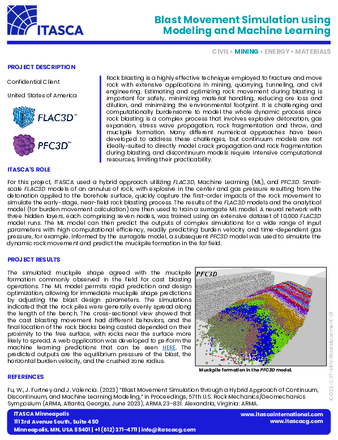
Blast Movement Simulation using Modeling and Machine Learning (2023)
Estimating and optimizing rock movement during blasting is important for safety, minimizing material handling, reducing ore loss and dilution, and minimizing the environmental footprint. ITASCA used a hybrid approach utilizing FLAC3D, Machine Learning (ML), and PFC3D to model the whole dynamic process of rock blasting that involves explosive detonation, gas expansion, stress wave propagation, rock fragmentation and throw, and muckpile formation.
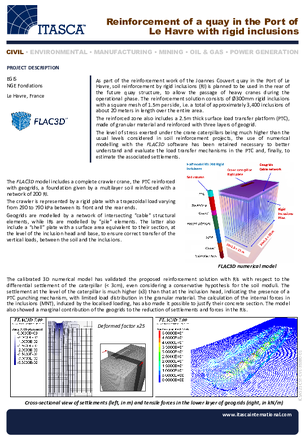
Reinforcement of a quay in the Port of Le Havre with rigid inclusions (2023)
As part of the reinforcement work of the Joannes Couvert quay in the Port of Le Havre, soil reinforcement by rigid inclusions (RI) is planned to be used in the rear of the future quay structure, to allow the passage of heavy cranes during the operational phase.
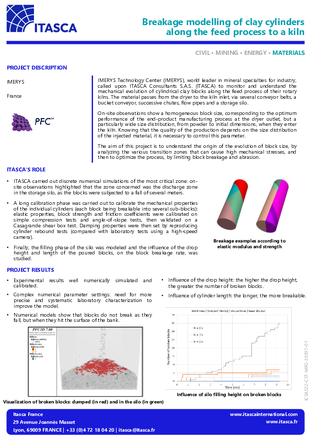
Breakage modelling of clay cylinders along the feed process to a kiln (2022)
IMERYS Technology Center (IMERYS), world leader in mineral specialties for industry, called upon ITASCA France (ITASCA) to monitor and understand the mechanical evolution of cylindrical clay blocks along the feed process of their rotary kilns. The material passes from the dryer to the kiln inlet, via several conveyor belts, a bucket conveyor, successive chutes, flow pipes and a storage silo.
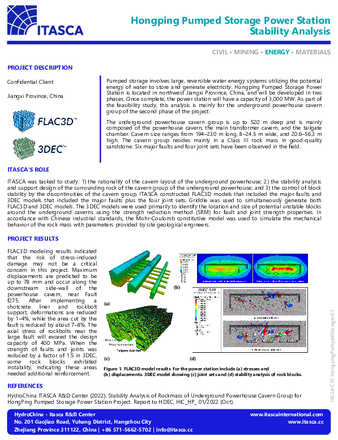
Hongping Pumped Storage Power Station Stability Analysis (2022)
Hongping Pumped Storage Power Station is located in northwest Jiangxi Province, China. Once complete, the power station will have a capacity of 3,000 MW. ITASCA's analysis focused on the underground powerhouse cavern group of the second phase of the project. The cavern group resides mainly in a Class III rock mass in good-quality sandstone. Six major faults and four joint sets have been observed in the field.
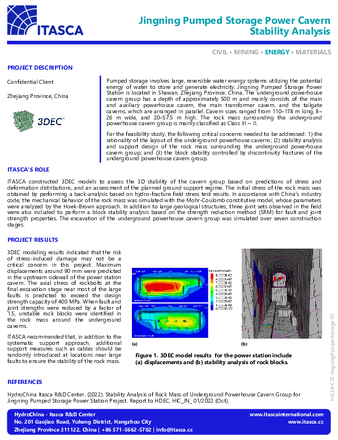
Jingning Pumped Storage Power Cavern Stability Analysis (2022)
ITASCA performed a feasibility study for the Jingning Pumped Storage Power Station(Zhejiang Province, China). The study included: 1) reviewing the layout of the underground powerhouse caverns; (2) stability analysis and support design of the rock mass surrounding the underground powerhouse cavern group; and (3) the block stability which is controlled by discontinuity fractures of the underground powerhouse cavern group.
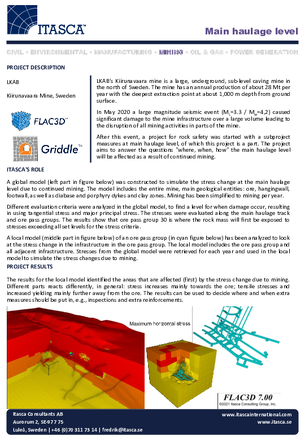
Main Haulage Level (2022)
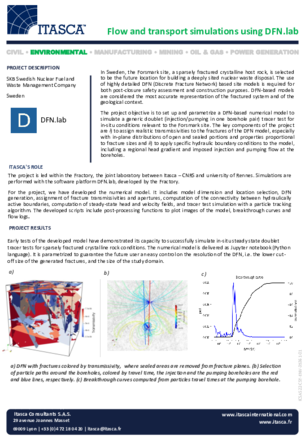
Flow and transport simulations using DFN.lab (2022)
In Sweden, the Forsmark site, a sparsely fractured crystalline host rock, is selected to be the future location for building a deeply sited nuclear waste disposal. The use of highly detailed DFN (Discrete Fracture Network) based site models is required for both post-closure safety assessment and construction purposes. DFN-based models are considered the most accurate representation of the fractured system and of the geological context.
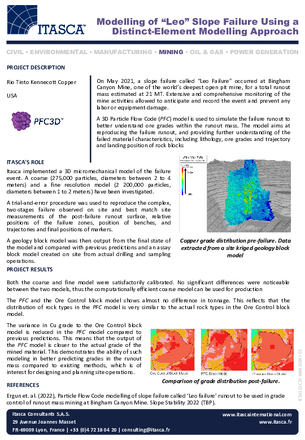
Modelling of “Leo” Slope Failure Using a Distinct-Element Modelling Approach (2022)
On May 2021, a slope failure called “Leo Failure” occurred at Bingham Canyon Mine, one of the world’s deepest open pit mine, for a total runout mass estimated at 21 MT. Extensive and comprehensive monitoring of the mine activities allowed to anticipate and record the event and prevent any labor or equipment damage.
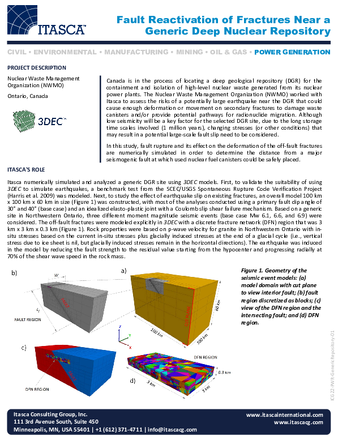
Fault Reactivation of Fractures Near a Generic Deep Nuclear Repository (2022)
The Nuclear Waste Management Organization (NWMO) worked with Itasca to assess the risks of a potentially large earthquake near a generic DGR that could cause enough deformation or movement on secondary fractures to damage waste canisters and/or provide potential pathways for radionuclide migration.
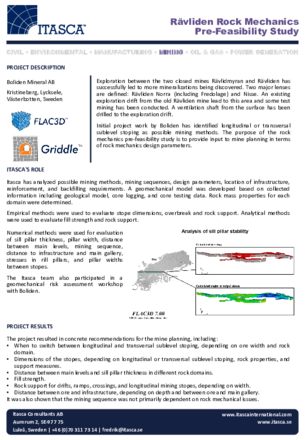
Rävliden Rock Mechanics Pre-Feasibility Study (2021)
Exploration between the two closed mines Rävlidmyran and Rävliden has
successfully led to more mineralizations being discovered. Itasca has analyzed possible mining methods, mining sequences, design parameters, location of infrastructure, reinforcement, and backfilling requirements. A
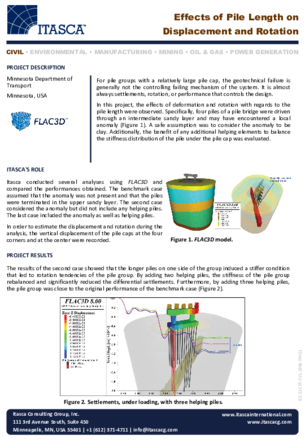
Effects of Pile Length on Displacement and Rotation (2021)
In this project, the effects of deformation and rotation with regards to the pile length were observed. Specifically, four piles of a pile bridge were driven through an intermediate sandy layer and may have encountered a local anomaly (Figure 1). A safe assumption was to consider the anomaly to be clay. Additionally, the benefit of any additional helping elements to balance the stiffness distribution of the pile under the pile cap was evaluated.
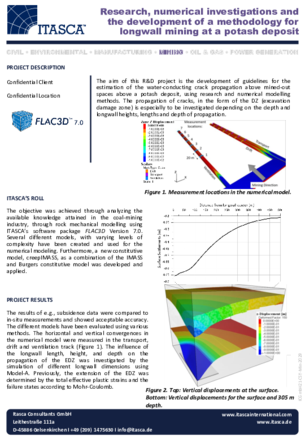
Research, Numerical Investigations and Development of a Methodology for Longwall Mining at a Potash Deposit (2021)
Aim of this R&D project is the development of guidelines for the estimation of the water-conducting crack propagation above mined-out spaces above a potash deposit, using research and numerical modelling methods.
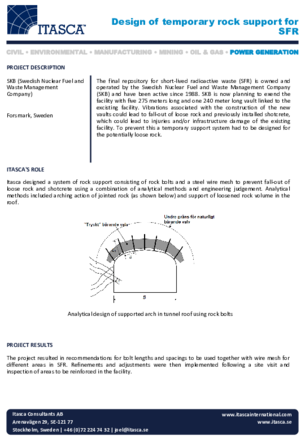
Design of temporary rock support for SFR (2021)
The Swedish Nuclear Fuel and Waste Management Company (SKB) is planning to extend the short-lived radioactive waste repository with five 275 meters long and one 240 meter long vault. Since the extension could lead to damage on the existing facility, Itasca designed a temporary support system to prevent loose rock.

Wind Turbine Foundation Analysis (2021)
In general, analysis performed on wind turbine foundations focus on the effects of the foundation’s rotational stiffness and deformation for a range of overturning moments. This project stage focused on the performance of the foundation and, given the local soil condition, its bearing capacity. To evaluate the behavior of the soil-structure interaction, a detailed numerical model of the concrete foundation and its steel reinforcement (i.e., rebar) was built and analyzed in FLAC3D.
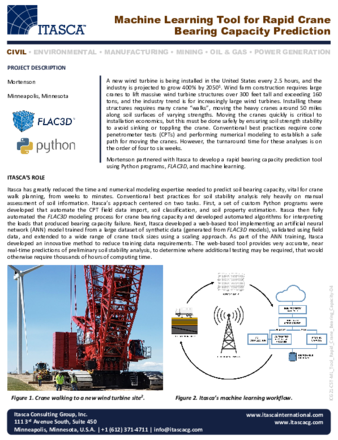
Machine Learning Tool for Rapid Crane Bearing Capacity Prediction (2021)
Wind farm construction requires large cranes to lift massive wind turbine structures over 300 feet tall and exceeding 160 tons. Installing these structures requires many crane “walks”, moving the heavy cranes around 50 miles along soil surfaces of varying strengths. Moving the cranes quickly is critical to installation economics, but this must be done safely by ensuring soil strength stability to avoid sinking or toppling the crane. Conventional best practices require cone penetrometer tests (CPTs) and performing numerical modeling to establish a safe path for moving the cranes requires on the order of four to six weeks. Itasca developed a rapid bearing capacity prediction tool using Python scripts, FLAC3D, and machine learning to provide near real-time feedback on the soil bearing capacity at a location, allowing enhanced crane walk planning.